
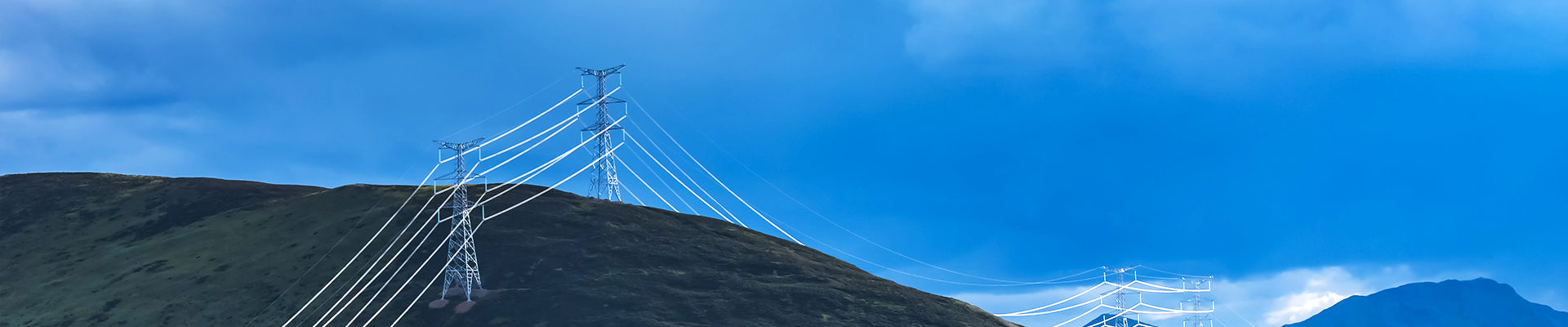
Quality Assurance
Technical specification
I. Product characteristics, quality standard
Main businesses for production of the company cover production of devices and components related with large-scaled road maintenance machinery. To enhance product quality assurance and clarify work task, scope and responsibility of product quality test, quality spot check mechanism in Tangshan Kuntie Technologies Co., Ltd. is hereby enacted. This mechanism is enforced throughout the company. Technology Quality Control Department is responsible for supervising the execution.
This mechanism incorporates: acceptance check management of raw materials, test and management of purchased parts, test and management of cooperation parts, production process inspection management, management of nonconforming goods and so forth.
II. Characteristics of raw materials and auxiliary materials and quality standards used for production
Raw materials of products mainly include metal materials and some rubber products. They should severely adhere to relevant standards on specification of materials during the manufacturing process.
III. Production process
Audit of drawing-preparation of production technique-issuing of procurement planning-procurement of raw materials-test of raw materials-production-acceptance check (self-check, mutual check (nonconforming disposal), special check), storage of components, assembly, test, punch marking of conforming goods
IV. Production technological flow
V. Production process specification
(1) Technological specifications on machine work
1. Machine work staffs should go through special training and possess fundamental knowledge on machinery and competence of machinery operation. They can satisfy various requirements proposed by existing product components on machinery processing.
1.1 Machine work device and technique should satisfy various existing requirements of products.
1.2 Measuring instrument used for machine work should be verified as conforming by the measurement department and should be within the specific calibration period.
2. Preparation before processing
2.1. After getting the processing task, operators should start by checking whether product samples, technological flows and relevant technological materials needed for processing are completed or not.
2.2. Machine work staffs should get acquainted with production samples and technological files in advance to check key components for part manufacturing and prepare all kinds of processing tools and measurement instruments following demands of processing.
2.3 Machine work staffs should apply conforming blank or semi-finished products before processing and check whether they conform to requirements of pattern. Processing is now allowed should one of the following cases arise:
a. Evident defects in processing workpiece.
b. Nonalignment of processing workpiece and size or shape of drawing.
2.4 Prepare all technological devices needed following requirements of technological procedure and timely disposal issues should they emerge. Get acquainted with use methods and operational methods of new clamps, model sand so on.
3. Tools and workpiece card mount
3.1 Card mount of cutters
3.1.1 Make sure that knife handle, cutter bar, guide sleeve and so forth are wiped clean before clamping various tools.
3.1.2 Fix the clamping following stipulations in the technological specifications. If technological specifications fail to specify clamping means, operators can opt for locating basis and clamping methods. Selection of locating basis should abide by the following rules.
a. Try to make sure alignment between locating basis and design basis.
b. Try to adopt the same locating basis for various processing panels. Benchmark for rough machining can be in use once.
c. Locating basis for precise processing should be carried out on the processing surface.
d. Locating basis should make sure that workpiece localization and card mount be convenient, stable and reliable during processing.
3.13. Positioning of joint panel should be heeded when clamping the assembling unit.
3.14. Acting point of clamping pressure should get through the supporting point or bearing surface when clamping the workpiece, carry out auxiliary backup in proper places for workpiece with inferior rigidity in order to enhance its rigidity.
3.15 Software such as red copper peel should be applied when clamping finish machining panel and workpiece with soft texture.
3.16 Supporting point of pressing plate should be slightly higher than workpiece surface that is pressed against. Compression bolt should try to press near to workpiece to ensure packing force.
4. Processing requirements
4.1 Processing staffs should strictly follow relevant requirements in production drawings and techniques to conduct processing on components.
4.2 Should inappropriateness arises in production pattern and technological files during the production process, processing staffs should timely report them to section chief in the workshop. But they are not allowed to alter patterns and files at their own will.
4.3 Processing should be carried out following middle tolerance should no special requirements be attached for processing of those with sizes having a requirements on tolerance.
4.4 Ra, known as surface roughness after processing, should not surpass 25μm for rough processing procedure that does not have requirements on surface roughness in work norms.
4.5 Choose reasonable cutting dosage following precision requirements of workpiece materials, machine tools, cutters, fixture and so forth in order to guarantee processing quality and boost productivity. Depth of cut should be higher than sand-adding layer or hardened layer when conditions allow it in order to avert damage of cutter by hardened layer of surface sandmark.
4.6 Ra datum, surface roughness value before accurate grinding, should not surpass 6.3μm.
4.7 Chamfer, rounding, groove depth and so on should be enhanced or deepened following precise processing during rough processing in order to make sure that designing requirements is aligned with after precise processing.
4.8 Chamfer, rounding, groove and requirements on allowance that fail to be specified in pattern and technological procedure should conform to requirements of GB1808.
4.9 Ra datum or surface roughness value of this procedural processing should not surpass 6.3μm for component surfaces that need surface hardening, ultrasonic flaw detection or roll finishing
4.10 Rag arising from processing of this procedure should be removed in the procedure of deflashing after this work procedure.
4.11 Timely check whether workpiece is loose or not during the processing procedure of major possessions in order to prevent processing quality or accidents due to looseness.
4.12 Should abnormal noise arise from machine bed-cutter-workpiece system or when processing surface roughness suddenly misfires during the cutting process, retract the cutter and halt the machine for inspection.
4.13 Carry out initial workpiece test in mass production and proceed with processing after conformity.
4.14 Operators should carry out self-check on workpiece during the processing process.
4.15 Correctly use measuring appliance during test. Push or screw gauge, micrometer and so on gently. Fierce push is not allowed. Null the measurement gauge in advance.
4.1.6 Locate waste and upgraded products arising during the processing process. Adulteration is not allowed.
5. Disposal after processing
5.1 Processing of each procedure of workpeice should be free from shaving, water or foul and should conform to specifications of instruments. They should be properly position in the region. Knocking, collision, scratching and so forth should be circumvented.
5.2 Rust prevention should be carried out on surfaces that not yet enter the follow-up procedure or after precise processing.
5.3 Demagnetization should be carried out after processing of workpiece processed by magnetic fixture.
5.4 Processing should be labeled for
5.5 Workpiece completed in each work procedure can enter the following work procedures after inspectors check them as qualifying.
6. Other requirements
6.1 Technological devices should be wiped clean (with anti-rust oil painted) and positioned in specific location or delivered to tools library.
6.2 Product design, technological regulations and other technical files in use should be kept clean. Alteration is not allowed.
(II) Weld procedure specifications.
1. Welder
1.1 Welders should take exam and get certificate before being engaged in welding of qualifying programs within the valid period.
1.2 Welders should get to know steel variety, welding materials and welding technological points before welding.
1.3 Welders should get acquainted with drawing and welding techniques prior to welding.
1.4 Check assembly quality and assembly requirement of weld groove to be welded. Refuse to weld welding joint that are not conforming to assembly quality and requirements and report that to relevant departments.
1.5 Carry out self-check on welding quality and carry out records on self-check, welding label or welding track.
2. Welding equipment
2.1 Choose welding machines following welding current and actual duty cycle needed for welding construction.
2.2 Each welding device should have grounding device to be grounded.
2.3 The welding device should work normally and be secured and reliable. Instruments should be verified as conforming.
3, Welding materials
3.1 Welding materials should be conforming products during stock. Re-test should be carried out should suspicion on texture arises. They can be in use after being checked as qualifying.
3.2 Carry out necessary drying disposal on welding bars following specifications on use of welding bar before welding.
3.3 Welding bar should be positioned in the heat preservation box with temperature at 100° and 150° and should be use whenever it is needed. Times of repetitive drying cannot run beyond 3 times.
4. Preparation before welding
4.1 Edge preparation: groove with tool carbon steel as the materials adopt cold machining or hot machining method.
4.2 Welding edge should align with pattern regulations.
4.3 Welding edge should be kept flat and should be free from such drawbacks as cracks, delamination, slag inclusion and so forth.
4.4 Remove such sundries as water, oxide, greasy dirt, rust, slag and so forth on the surface and at the two sides of edge before welding. Cleaning scope: surface and two sides of edge of welding seam (scope of 20 mm width around the edge) Fillet weld, weld leg size K=10mm,20mm
5. Welding environment
5.1 Welding is only allowed after the following conditions are satisfied.
a)Wind speed:<10m/s
b)Relative moisture <90%
c)Welding temperature higher than -10℃
6. Preheat
6.1 When the weldment temperature is lower than 0℃, it should preheated to above 15℃ within a width scope of 100 mm.
6.2 When partial preheat is adopted, preheat scope covers two sides of the welding joint and should be no less than 3 folds of weldment thickness. It should be no less than 100mm.
7. Positioned weld
7.1 Welding materials used for positioned weld should be consistent with welding material designation adopted by South Korea.
7.2 Thickness of positioned welding is no bigger than half of the welding. It is usually at 4mm and 6mm with interval no more than 400 mm.
8. Basic requirements on welding
8.1 Welding is conducted following pattern, technological document and technological standards.
8.2 Adjust welding parameters following welding procedure card prior to construction. Do not adjust welding parameters on the welding products.
8.3 Frock clamp can be in use with reasonable welding procedures adopted for weld assembly prone to be deformed.
8.4 All defects that would affect welding of the following welding joint should be removed during the re-welding procedure.
8.5 Complete penetration and fusion should be guaranteed in the arc connection.
8.6 When hammering is in use to improve welding quality, the first box cover layer cannot be hammered.
8.7 Welding slag and weld spatter should be removed after welding and check appearance quality.
9. Shape righting, after heat of weldment and disposal to relieve stress
9.1 Shape righting of weldment
Mechanical methods should be adopted for righting shape. When partial heating method is adopted for righting shape, temperature of its heating zone should be constrained at below 800℃.
10. After-sales services
10.1 Repair is allowed for welding connector. Quality analysis should be done on crack arising from welding before seeking out the reasons and drawing out measures for repair.
10.2 Wipe clean defects prior to repair and adopt surface flaw detection for determination when necessary.
10.3 Requirements for welding quality of repair are consistent with the raw welding joint.
10.4 Workpiece requiring heat disposals can go through heat disposal when necessary during repair after heat disposal.
11. Safety production
11.1 Welding operation should conform to relevant requirements in GB9448.
11.2 Welding staffs should receive education on safety and hygiene and master safety production technologies.
11.3 Welding staffs should be cladded with necessary protection tools.
11.4 Welding construction fields should be installed with safety facilities against electric shock, fire hazards and toxication. It should be ventilated. Welding should be carried out within the battle in order to prevent impacts imposed on people by arc light and splashing.
(III) Assembly technological regulations
1. Normal requirements
1.1 All components should be deflashed with their acute angles abated. Knock, bump, scratching and others that would affect usage performance are not allowed. Trimming should be removed for ‘O’-shaped circle and other rubber sealed components and sealing should not be affected.
1.2 Components or purchased goods should be checked as conforming by Quality Check Department before being put into use.
1.3 All metallic components should be wiped clean by diesel oil. Scrap iron, rust, grease or spoil are not allowed.
1.4 Take and position them gently during the assembly process. Brute operation is not allowed. Sealing surface of components is not allowed. Do not cut rubber seals.
2. Before assembling process, carefully read product assembly drawing, technological requirements for assembly and test procedure for assembly. Get acquainted with structural characteristics of products. Get hold of procedures for product assembly, assembly methods and requirements for assembly for each step.
3. Prepare completed assembly tools, take all components needed, position small components on clean work desks and important components in the working position apparatus kit.
4. Test after assembly
Check whether assemble is correct or not after assembly. Check whether neglected package or extra package exists.
5. After assembly
Sign the name of operators and inspectors as well as date for assembly test in the assembly trial sheet.
6. Production of components
1) Technologists of the Department of Technological Quality carry out technological designing of products following product drawing and technological files.
2) After technological design is over, verification is carried out by production workshops and relevant departments organized by Department of Technological Quality. Relevant records should be done and technological designing should be perfected;
3) After reveal and approval by technological files, the Department of Technological Quality would officially issue official technological files following requirements. Department of Technological Management is responsible for classification following requirements;
4) Production workshops execute technological files for manufacturing of products and strictly enforce regulations for discipline management of on-spot technologies for production.
Focus on us
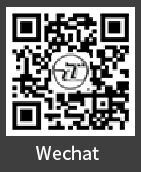
National service hotline
Addr:No. 15 Shizhuang Street, Lunan District, Tangshan City
Office phone:+86-315-5655228
Copyright © 2019 All Rights Reserved Tangshan Zhongtie Industry Co., Ltd.